top of page
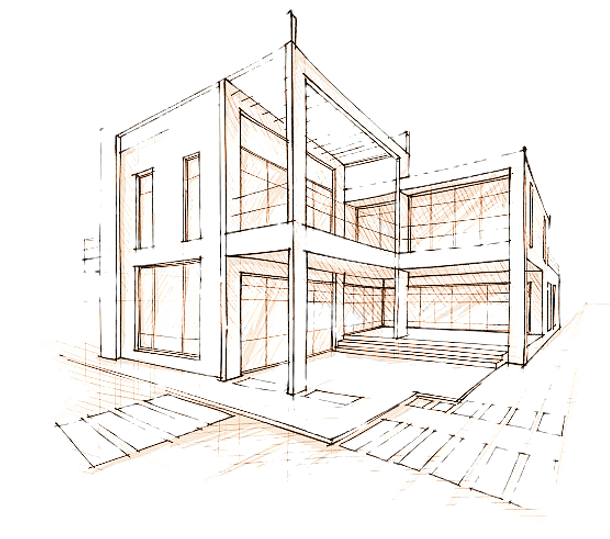
.png)
Buildings viewed up close by VG Expert
Your partners in construction expertise
Assistance VO in private and communal & Expertise construction errors and damage, also problems with contractors and architects, misleading sale of a home, technical advisor in legal proceedings, etc.
Please call or email us - 0472 59 18 98
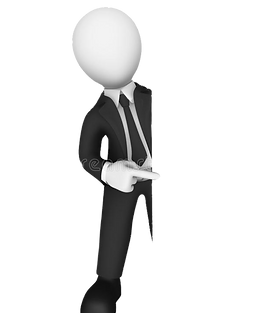


.png)
Norms-Antenna Tolerances and Views (Eye Precision)
(Excerpt from BBRI publication www.norms.be/tolerances)
Tolerances in construction
Why tolerances?
The construction plans or a 3D model of a building reflect the ideal state envisaged during the design. A straight line is straight, the position of a facade opening is accurately represented down to the millimeter and every connection is perfect.
During the implementation, one is confronted with reality: measuring errors and human errors inevitably occur, construction elements show a certain dimensional variability, colors often dare to deviate, and so on. Thus, deviations are induced in the structure.
On the other hand, there are also unavoidable dimensional changes that occur due to movements and the changing size of materials in response to changes in environmental conditions. While it goes without saying that these variances are inherent to the build process, this is sometimes reflected in the review.
eye lost.
In short, the situation actually built will differ from the plans or model. Especially when one is fixated on the perfection of the plans and models, this gives rise to disappointment and discussion.
Tolerances in practice
Despite the existence of these series of standards, “tolerances in construction” remains a very extensive and difficult subject. Where there is a jungle of regulations or standards for certain aspects – which can say different things – other aspects have to be judged subjectively due to a lack of concrete criteria.
Contractual documents also do not always provide the desired clarity. Possible problems on the construction site are therefore often ultimately reduced to an assessment of whether or not work was carried out (in)carefully, based on a single check at the end of the construction process.
Such a check must be carried out with a sufficient dose of common sense. After all, in the execution of a construction work – whether it concerns the manufacture, the assembly or the measurement itself – there is one certainty: inaccuracies and imperfections will occur.
Care must therefore be taken from the design stage that the set of requirements is realistic, that dimensional variability is taken into account and that the assessment method is in line with the practical implementation.
Performing a visual assessment of an element
Certain view features are assessed visually. For example, it may concern color differences, irregularities in floors and plaster, light damage, etc. Since such visual assessments are often subjective, tools can be used to carry out a more objective evaluation.
Circumstances
The appearance of a surface should always be assessed with the naked eye, under normal incidence of light and from a specific distance (depending on the element to be checked). Under no circumstances may this assessment be carried out under glancing light or in backlighting.
For vertical surfaces, the assessment distance is generally 2 m (indoors) or 3 m (outdoors). The delivery of floor finishes is perpendicular to the surface to be inspected and from man's height (with a minimum distance of 1.5 m).
The appearance of a building may only be assessed after it has dried sufficiently, in order to avoid noticing color differences that are typical for the drying period.
Finish
Given the multifaceted aspects within the domain of building finishing, the reference documents and standards relating to this are particularly numerous. The relevant documents and explanations(*) aim at the tolerance on the finishing elements (including floor coverings, plasters, roof coverings,
painting, joinery, etc.) from the standards and to explain.
We would like to point out that the most recent version of the standard should always be consulted, the content of which takes precedence over those on our website. The measurement methods that are explained are measurement methods that can be used on site.
bottom of page